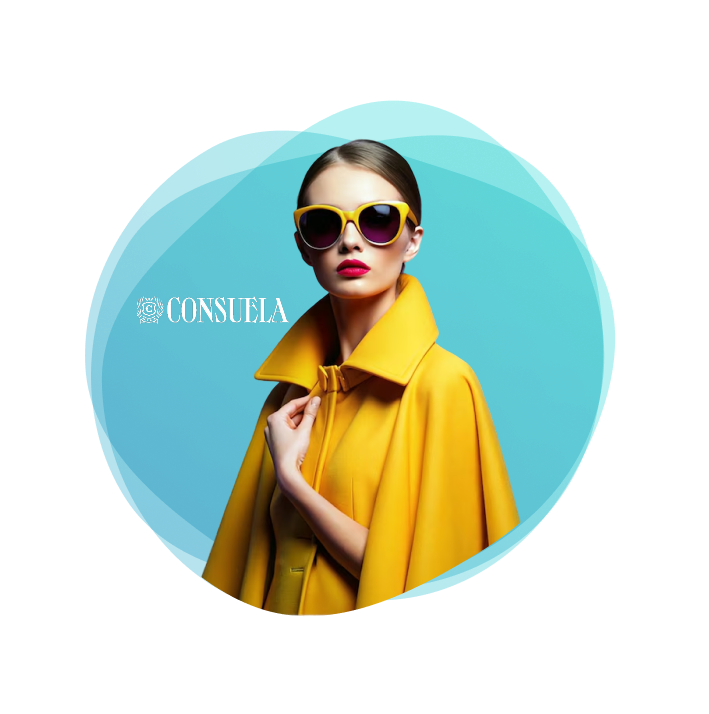
Customers
Users
Countries
Years of Success
Discover how Aquarelle, a leading apparel manufacturer, optimized its operations, streamlined workflows, and secured data across locations with WFX ERP.
Read full storyDiscover how Shimano optimized global apparel development processes, improved compliance, and minimized manual work with WFX PLM’s robust, web-based solution.
Read full storyDiscover how Clare V., a Los Angeles-based handbag and accessories brand, streamlined product development processes and costing with WFX PLM, improving data management, collaboration, and overall efficiency.
Read full storyDiscover how SAS DUDES leveraged WFX PLM to streamline their product development processes, enhancing efficiency and boosting creative output in their distinctive fashion lines.
Read full storyDiscover how Feetures, a leading US running socks brand, streamlined operations and enhanced collaboration with WFX PLM, propelling their focus on global market leadership.
Read full storyDiscover how SAPL Industries Private Limited enhanced their operational efficiency, data security, and scalability by implementing WFX Apparel ERP.
Read full storyExplore how Consuela, the vibrant Austin-based handbag brand, transformed its design, development, and vendor collaboration processes with WFX Fashion PLM.
Read full storyDiscover how American luxury footwear brand Sarah Flint transformed its operational and strategic processes with the innovative WFX PLM system.
Read full storyExplore how Compressport revolutionized its product development and vendor collaboration with WFX PLM, streamlining operations and enhancing efficiency.
Read full storyDiscover how Vermont Teddy Bear revolutionized its vendor collaboration and streamlined operations with the innovative WFX PLM system.
Read full storyDCK Group's adoption of WFX PLM has significantly increased efficiency, productivity, and streamlined communication. With WFX, DCK has reduced manual functions and saved time, allowing teams to focus on more important tasks such as planning and product development.
Read full storyImplementing a PLM solution during the pandemic is no easy feat but Showpo and WFX made it work, going from strength to strength as a team, to roll-out the solution in a phased manner.
Read full storyQuay Australia sought a cloud-based PLM to streamline product development and collaboration. After thorough evaluation, they chose WFX—a perfect fit for their needs.
Read full storySee how OAK + FORT boosted production and expanded product categories with WFX, streamlining operations and driving business growth.
Read full storyWith WFX ERP, Bhartiya Fashion manages their entire business process from one platform with complete visibility into their entire supply chain which enables them to achieve greater efficiencies across all functions.
Read full storyAfter exploring options, RYU chose WFX PLM—the only cloud solution meeting all their needs. It’s customizable, user-friendly, integrates seamlessly, and enables real-time collaboration.
Read full storyRainwear began its journey with WFX by implementing the ERP in its apparel units. They soon realized the benefits of the system and decided to implement it in their machine manufacturing units as well.
Read full storyTexport lacked centralized coordination and relied on manual processes. WFX digitized their operations, streamlined communication, and improved visibility, cutting errors by 35% and data redundancy by 85%.
Read full storyPPJ struggled with integration, visibility, and compliance across 24+ factories. WFX helped streamline operations, ensure data accuracy, track costs, and improve deadline management in real time.
Read full storyBefore WFX, Pro Sports relied on a manual system, wasting time and money. With WFX, they’ve automated operations, improved visibility, and optimized costs with data-driven decisions.
Read full storyCrossline’s manual processes led to duplication, delays, and errors. With WFX, they streamlined operations, improved visibility, cut lead time by 25%, and boosted efficiency by 30%.
Read full storyGorjana relied on scattered spreadsheets, slowing product development. With WFX, they scaled efficiently, expanded into D2C retail, and streamlined remote collaboration during COVID.
Read full storyBenetton India’s lack of tracking led to delays and high costs. With WFX, they cut errors by 90%, improved vendor insights, streamlined communication, and reduced lead times by 35%.
Read full storyNINE&Co struggled with scattered data and poor collaboration. WFX centralized operations, improved decision-making, enabled 3D design integration, and cut lead times from 15 months to 12-14 weeks.
Read full storySpell’s scattered data led to inefficiencies and long cycles. With WFX, they streamlined operations, cut errors by 95%, reduced revisions, and boosted time-to-market by 30%.
Read full storySynergy struggled with data coordination and loss. With WFX Cloud, they ensured business continuity, cut errors by 70%, reduced redundancy by 80%, and improved delivery time by 10%.
Read full storyELK’s design team struggled with manual processes. With WFX, they boosted supply chain productivity by 35%, cut sample development time by 50%, and improved efficiency and transparency by 85%.
Read full storyForever New’s supply chain gaps slowed growth. With WFX, they increased transparency, cut concept-to-production time by 40%, reduced manual work, and centralized data for global expansion.
Read full storyEAM Maliban streamlined operations with WFX, cutting manual tasks, boosting productivity by 50%, reducing lead time by 20%, lowering material costs by 5%, and enabling data-driven decisions.
Read full storyOKA streamlined global expansion with WFX, improving efficiency by 40%, enhancing collaboration, and standardizing processes. Now thriving in the U.S., product quality has improved by 70%.
Read full storyNWF streamlined operations with WFX, cutting manual tasks by 25%, reducing wait times by 20%, and gaining full supply chain visibility—boosting efficiency, quality control, and export growth.
Read full storyDo you want to see how?